Table of Contents
The emergence of 3D designs and 3D modeling has paved the way for revolutionary advancements. One such groundbreaking innovation is the rise of Digital Twins.
The industry is taking the concept of virtual mirrors to new heights and providing fundamental insights into the design process.
This transformative technology has gained momentum across various industries. It offers a dynamic approach to design engineering and design process automation services.
What are Digital Twins?
Digital Twins are virtual replicas of physical objects or systems created through 3D CAD engineering software. These replicas mirror the visual aspects, emulating the behavior and characteristics of their real-world counterparts.
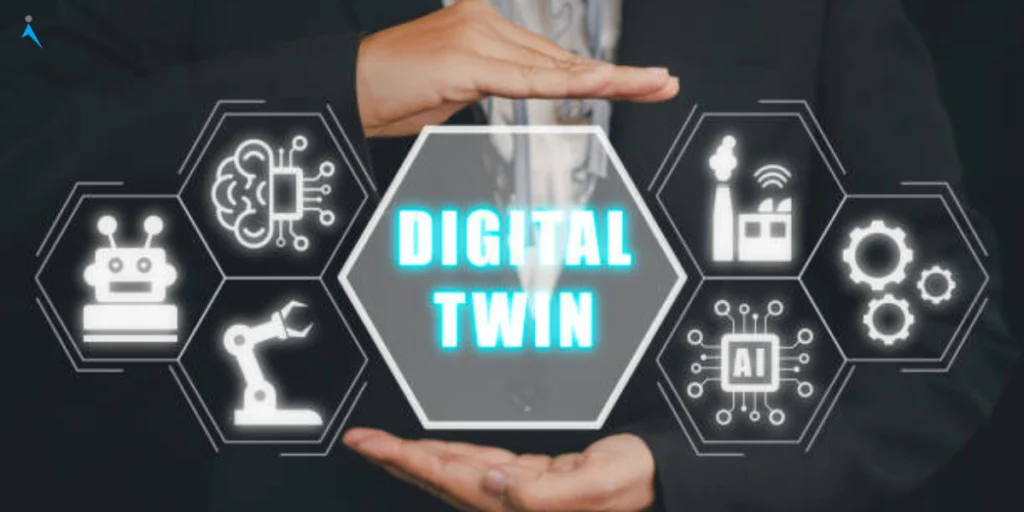
Utilizing digital twins solutions empowers manufacturing companies to simulate real-world scenarios. Their corresponding outcomes provide invaluable insights for informed decision-making.
This technology allows designers and engineers to comprehensively understand a product’s performance and behavior before it even exists in the physical world.
Types of Digital Twins
- Component twins/Parts twins
- Asset twins
- System or Unit twins
- Process twins
The Initial Use of Digital Twins as Virtual Mirrors
Initially employed as virtual mirrors, it served as precise replicas, aiding in visualizing and refining designs. Designers utilized 3D modeling to create virtual prototypes.
It enabled them to identify potential flaws and make necessary adjustments before moving forward with the physical manufacturing process. This virtual mirroring concept significantly reduced the risk of errors and improved overall design accuracy.
Transformation to Real Insights
The evolution goes beyond mere replication; it now encompasses the generation of real insights. Modern Digital Twins integrate advanced analytics, artificial intelligence, and machine learning algorithms.
It enables engineers to simulate real-world scenarios. This transformation empowers decision-makers to anticipate performance under various conditions and optimize designs. It ultimately enhances the overall efficiency of the product life cycle.
Key Components of Modern Digital Twins
Data Integration: Seamless incorporation of real-time data from sensors and IoT devices for accurate representation.
Advanced Analytics: Implementing sophisticated algorithms to analyze and interpret data enables comprehensive insights.
Machine Learning Algorithms: Integration of machine learning models for continuous improvement and adaptability to evolving conditions.
Visualization Tools: User-friendly interface and visualization tools that enhance accessibility and interpretation of complex digital twin data.
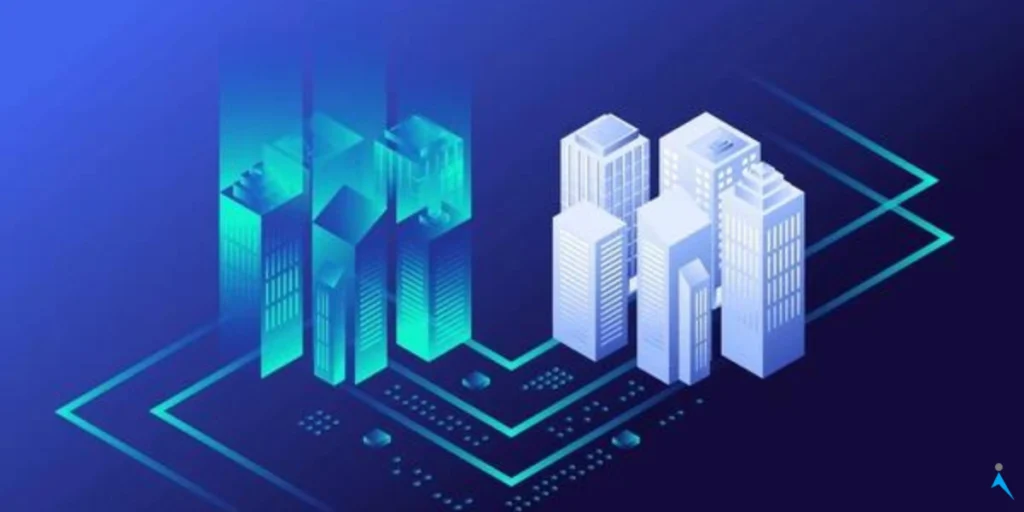
Interconnectivity: Facilitation of communication between various digital twins and systems, fostering a better understanding of interconnected processes.
The synergy of these elements facilitates the creation of accurate virtual models and ensures seamless integration with data analytics for actionable insights. The result is a holistic approach to product development that minimizes risks and maximizes efficiency.
What are the advantages of Digital Twins?
The advantages of adopting Digital Twins in the design and engineering process are multifold.
- It significantly reduces time-to-market by allowing rapid prototyping and iterations.
- It enables predictive maintenance, as Digital Twins can simulate the aging process of products. It aids in identifying potential failures before they occur.
- This technology enhances team collaboration by providing a shared virtual space for design discussions and modifications.
- Utilizing digital twins enhances the efficiency of product research and design by generating ample data on potential performance results.
Applications and Industries Leading the Way
Digital Twins have found applications across diverse industries, from manufacturing and healthcare to aerospace and automotive.
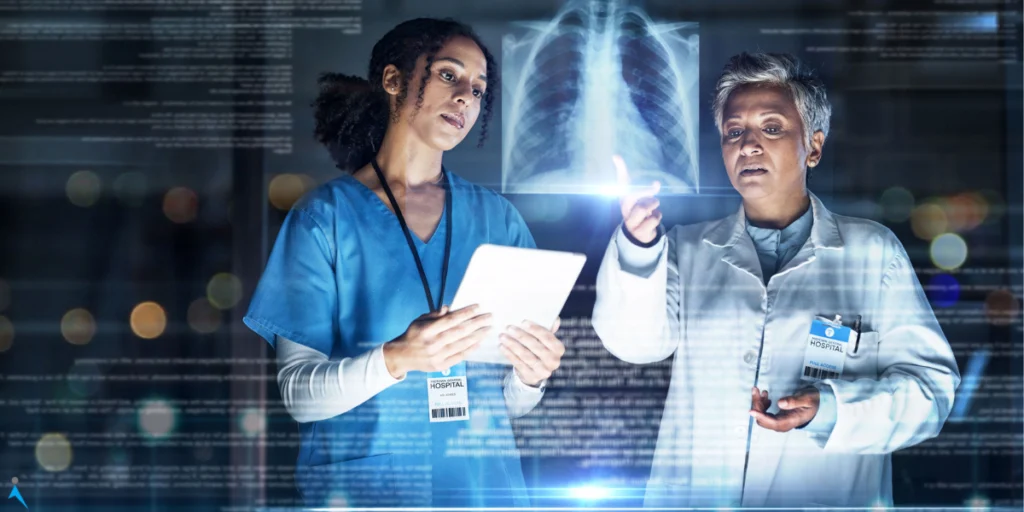
- In manufacturing, it streamline production processes,
- While in healthcare, they facilitate the development of personalized medical devices.
- The aerospace and automotive sectors leverage it to optimize vehicle performance and enhance safety measures.
- Singapore pioneered the development of a Digital Twin, using 3D mapping to address land scarcity and flooding risks. Virtual Singapore, created using advanced technology, offers a detailed 3D representation. Currently, the SLA is extending this initiative to create a subsurface digital twin of the entire nation.
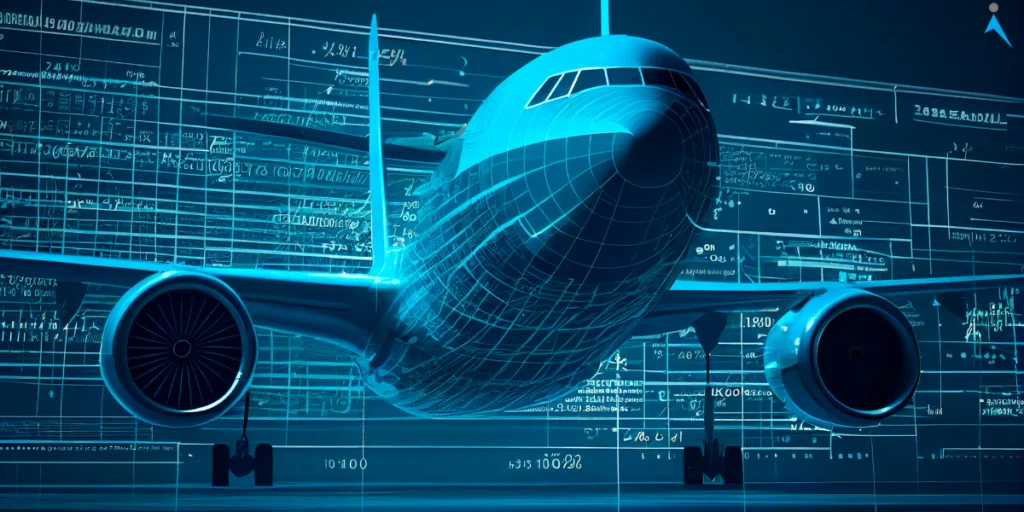
Digital Twins Solution with Immersiv Technologies
The potential of digital twins is boundless as a growing amount of cognitive power is dedicated to their utilization.
With continuous learning and evolving capabilities, digital twins technology is poised to provide valuable insights consistently. It will contribute to the enhancement of products and the efficiency of processes in the future.
An organization fostering a robust digital-twin network has the opportunity to integrate additional technologies, paving the way for the creation of an enterprise metaverse. The future holds the promise of a transformative and interconnected landscape.
Learn how the change will impact your industry – immerse yourself in the future with Immersiv Technologies.